活用分野一覧
-
- 水処理分野
- 工業用水から家庭用水・飲料水まで、用途によって求められる滅菌、殺菌といった水処理を、高精度な制御技術で実現します。
-
-
- 新エネルギー分野
- 燃料電池をはじめ、二次電池、太陽電池など、次世代エネルギー技術に貢献する製品を、イワキは用意しています。
- おもな活用分野
-
- 食品分野
- 厳格な衛生基準が設けられる食品分野で、移送、混合・調合、洗浄プロセス等に安全・安心をお届けします。
- おもな活用分野
-
-
-
-
- 半導体・液晶分野
- パーティクルの発生・混入のない、極めてクリーンな環境を要求される半導体プロセス。イワキのポンプ技術は、ここでも生かされています。
- 分野別ソリューション
- Q&A方式で、ケミカルポンプに関するお悩みを解決するソリューションをご紹介します。
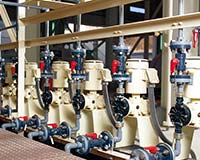